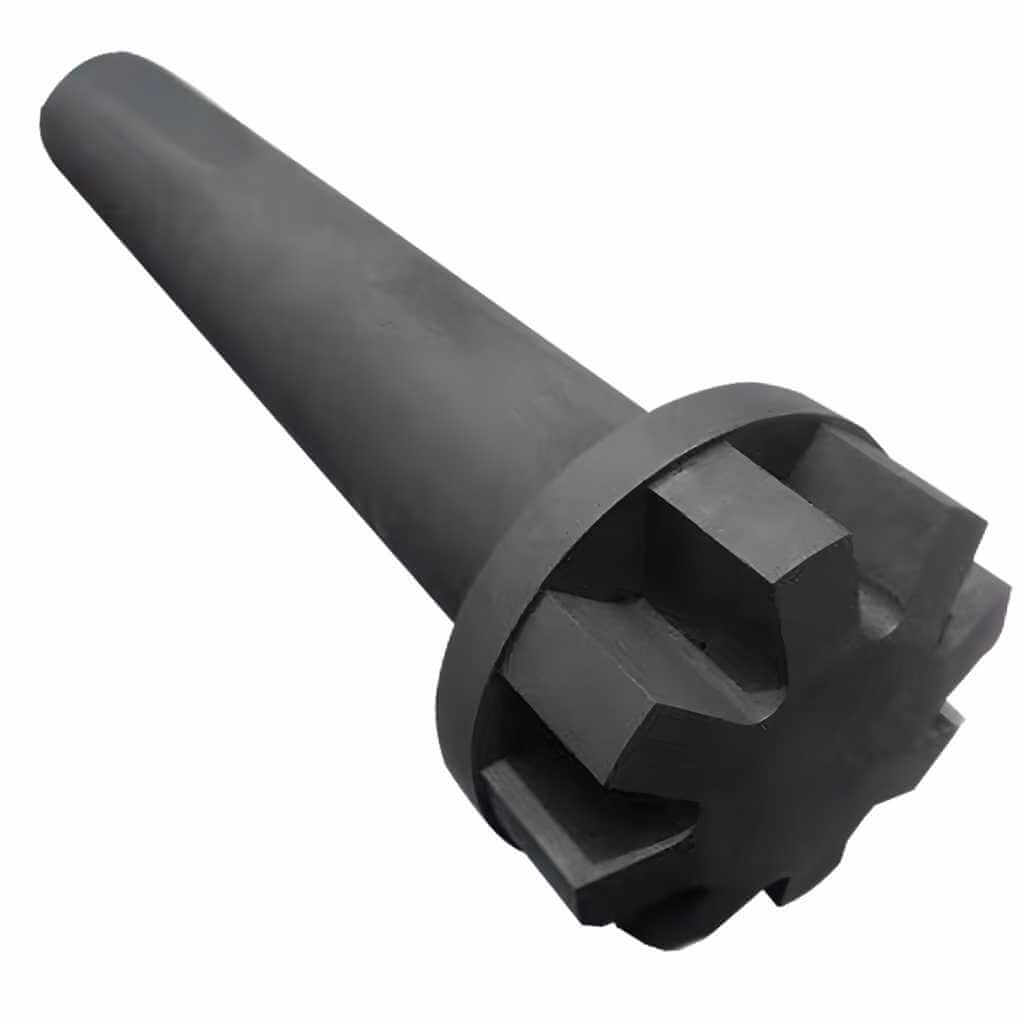
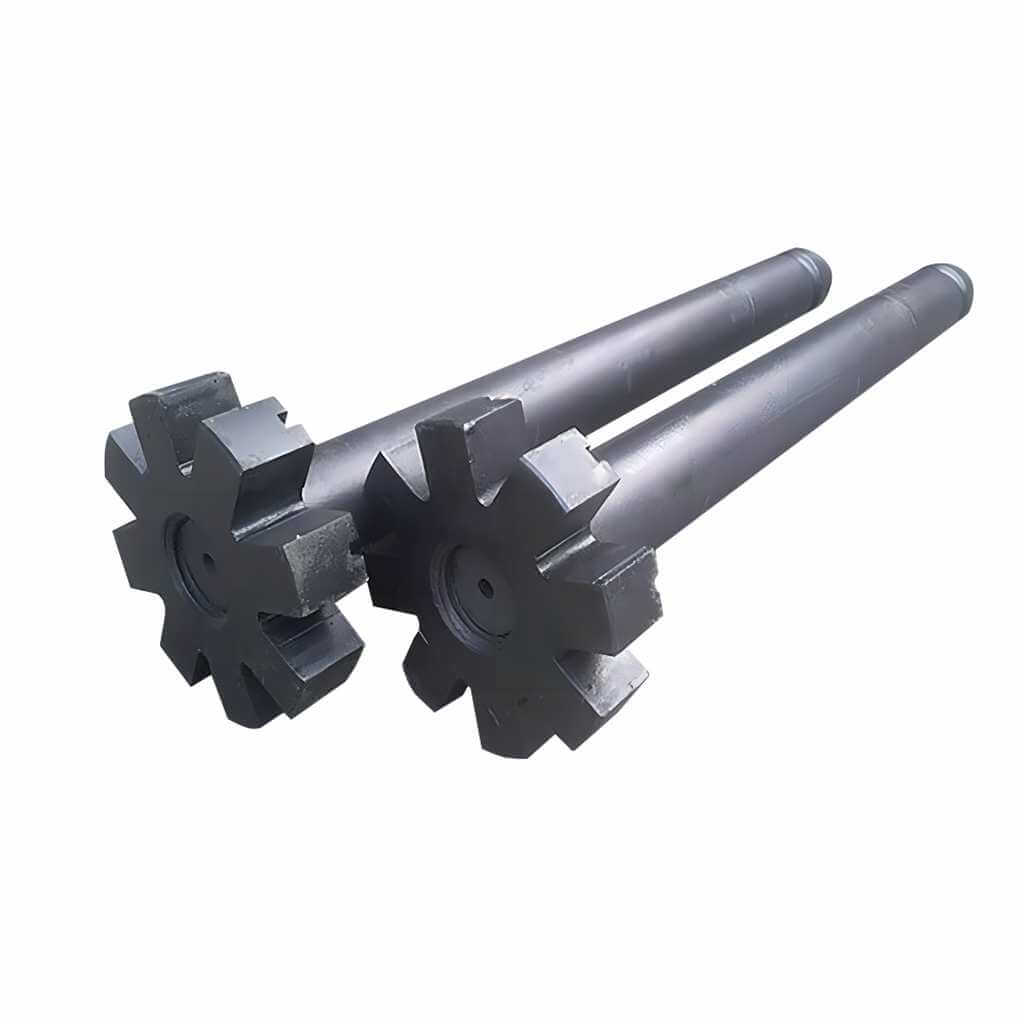
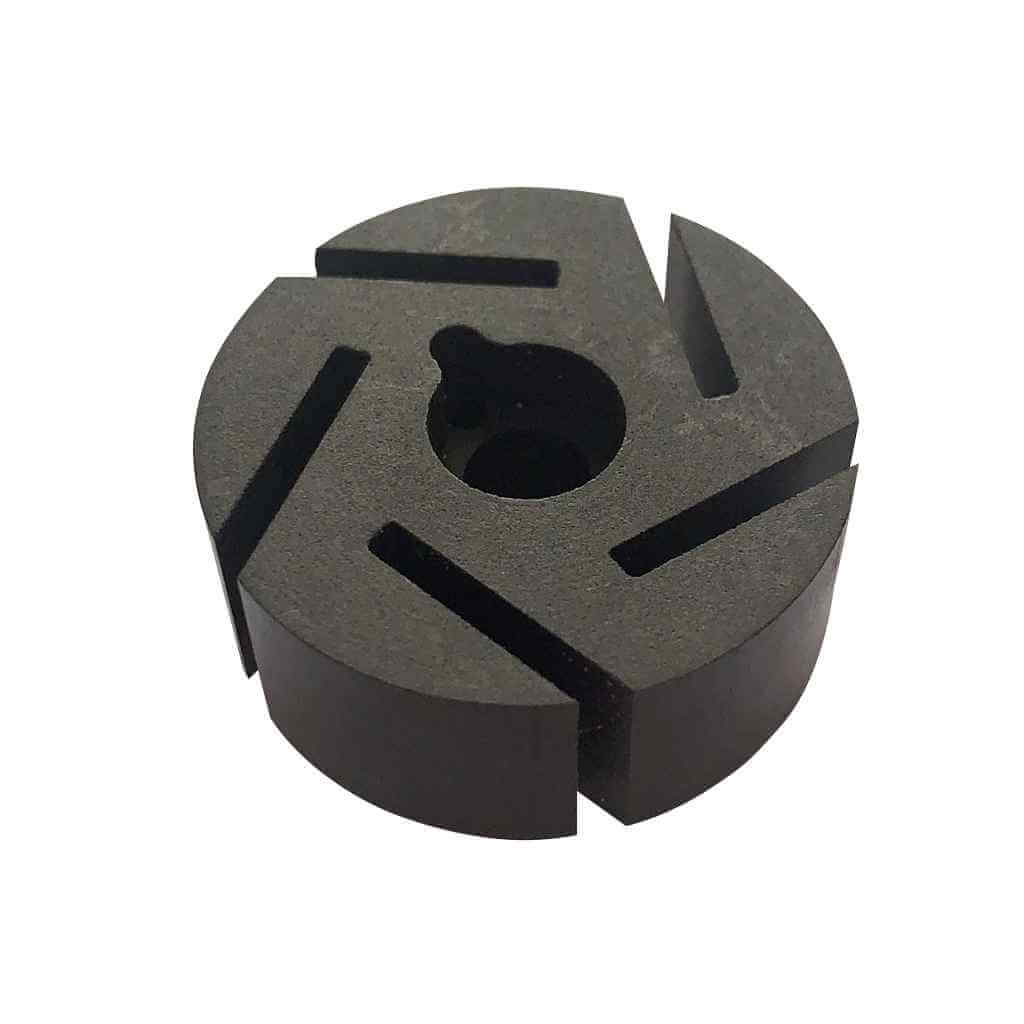
Graphite Rotors
FRANLI Graphite rotors are critical components used in aluminum alloy smelting equipment, playing a vital role in the degassing and fluxing operations of the smelting process. Comprising rotor poles and nozzles, graphite rotors are designed to withstand high temperatures and harsh chemical environments, making them essential for efficient and effective aluminum degassing.
Request a quoteGraphite rotors are a critical component of aluminum alloy smelting equipment, specifically designed to facilitate the degassing process. During aluminum alloy smelting, hydrogen and oxidation residues are produced, which must be purified and removed by a refining degasser, with the graphite rotor being an indispensable accessory of the slag machine.
The graphite rotor consists of a rotor rod and a nozzle and is made from impregnated high-purity molded graphite with special anti-oxidation treatments, resulting in a surface that is treated to extend its service life. It is widely used in the aluminum alloy casting industry due to its high-temperature resistance, oxidation resistance, and durability.
The manufacturing process of graphite rotors involves the use of special graphite as raw material, resulting in a product with high strength, high hardness, oxidation resistance, and low porosity. The rotor is carefully designed to withstand the harsh conditions of the aluminum alloy smelting process, including exposure to high temperatures and chemical reactions. The unique properties of the graphite rotor, such as its high-temperature resistance, oxidation resistance, and durability, make it an essential component for the efficient and reliable degassing of aluminum alloys.
The operation of using a graphite rotor requires preheating before use to avoid oxidation and ensure the longevity of the rotor. Once preheated, the graphite rotor is immersed in the aluminum liquid in the degassing box, where it rotates at a specific speed to stir the aluminum liquid and facilitate the degassing process. The use of a graphite rotor contributes to the production of high-quality aluminum alloys by effectively removing impurities and ensuring the integrity of the final product.
Graphite rotors, composed of high-grade graphite materials, have gained significant popularity due to their exceptional thermal conductivity, lightweight construction, and superior strength. These unique properties make graphite rotors an ideal choice for multiple industrial sectors, including automotive, aerospace, power generation, and more.
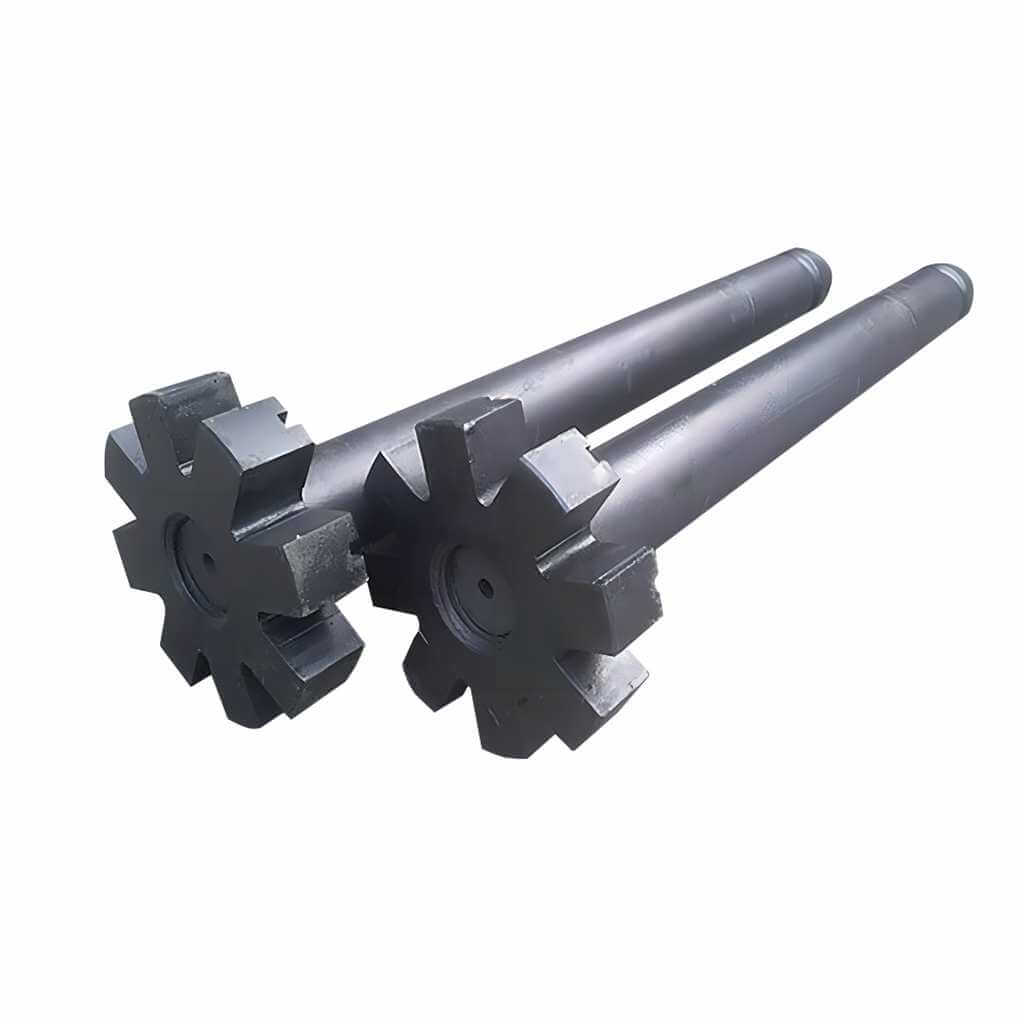
Automotive Applications:
In the automotive industry, graphite rotors are widely recognized for their exceptional heat dissipation capabilities, which contribute to improved braking performance, reduced wear and tear, and overall enhanced safety. Furthermore, their lightweight properties allow for reduced energy consumption, thereby enabling greater fuel efficiency and sustainability in vehicles.
Aerospace Applications:
In the aerospace domain, where weight reduction is crucial, graphite rotors have emerged as a game-changer. Their lightweight construction not only contributes to fuel efficiency but also enables enhanced maneuverability. Moreover, the high thermal conductivity of graphite rotors ensures efficient heat dissipation, making them an excellent choice for critical components in aircraft engines and braking systems.
Power Generation and Industrial Applications:
Graphite rotors have revolutionized power generation and industrial sectors by offering efficient and cost-effective solutions. Their ability to withstand high temperatures and resist corrosion makes them ideal for use in turbines, compressors, and various heavy machinery applications. Furthermore, their longevity and low maintenance requirements offer substantial cost savings for businesses.
Future Prospects and Advancements:
As technology continues to advance, researchers and manufacturers are exploring new ways to enhance the properties of graphite rotors further. Advancements in manufacturing techniques, such as 3D printing, are expanding the possibilities, enabling the creation of complex rotor designs with improved efficiency and performance.
Graphite rotors have proven to be an invaluable innovation across multiple industries, thanks to their exceptional thermal conductivity, lightweight construction, and superior strength. Whether in the automotive, aerospace, or power generation sectors, their versatile applications have brought about significant advancements, improving performance, efficiency, and overall sustainability. As we look toward the future, the evolving landscape of technology holds further promises for graphite rotors, making them an integral component in achieving excellence across various sectors.