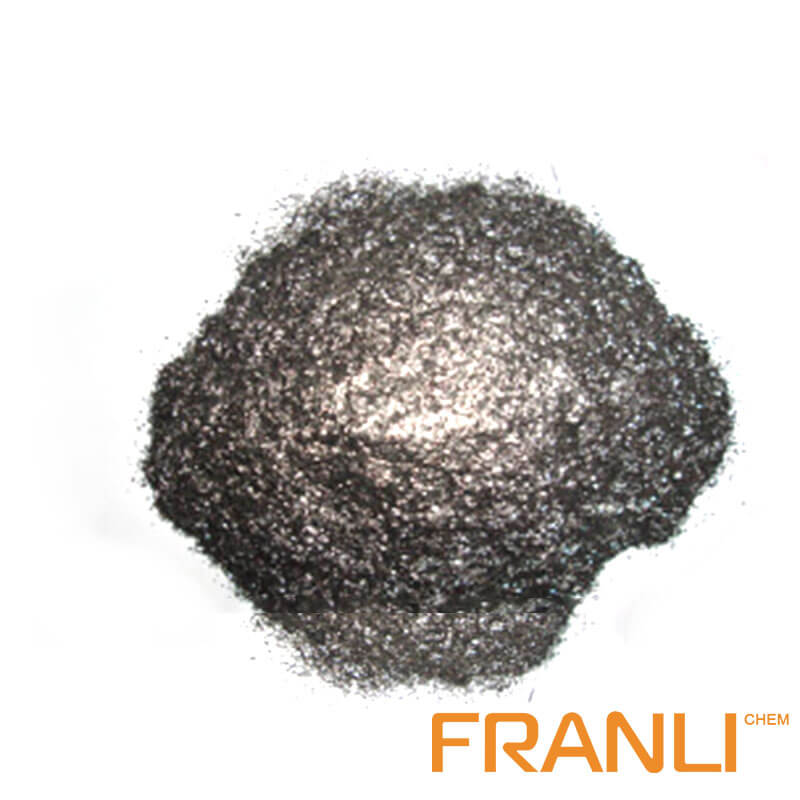
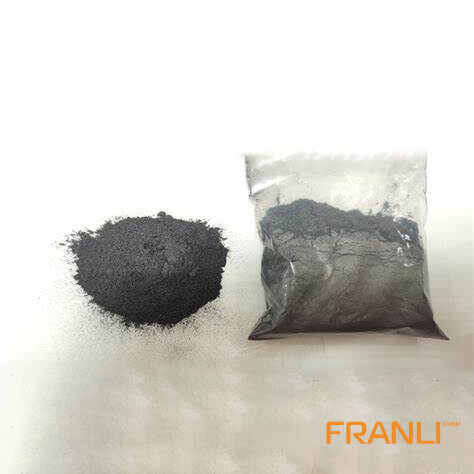
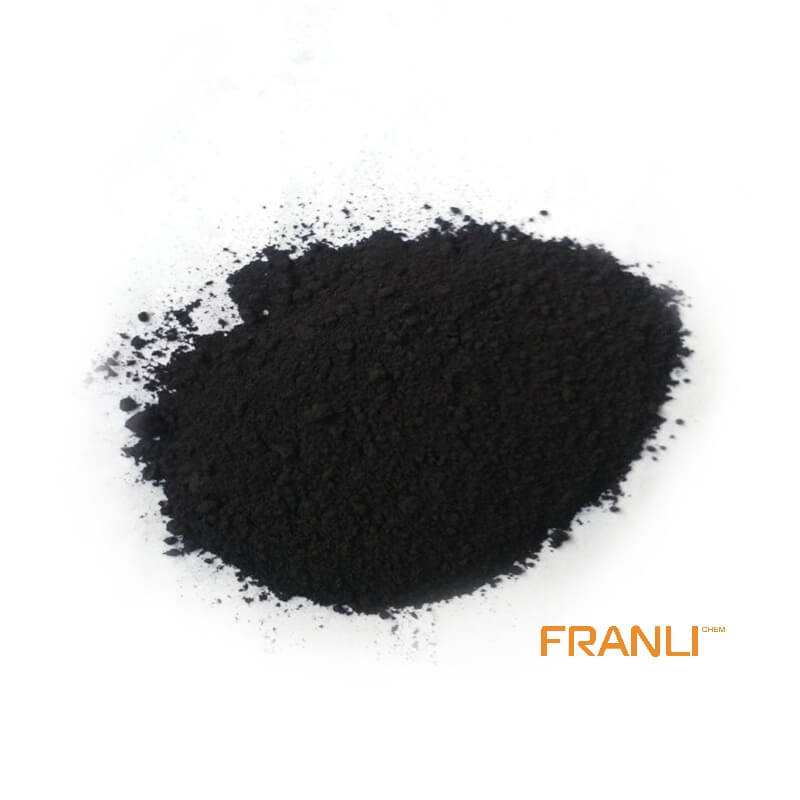
Flake Graphite
Size
0.01mm
Carbon Content
99%min
Package
25kg small bags into ton bags
Origin
China
Features
thermal shock resistance, lubricity, conductivity and plasticity…
Application
Lead battery plates positive and negative conductive agent, lithium batteries nickel hydrogen etc
Natural flake graphite has superior physical and chemical properties and is widely used in metallurgy, coatings and refractory industries. It is an important non-metallic raw material that is indispensable for today’s high-tech. Flake graphite is divided into large flake graphite and fine flake graphite according to the size of its scales. Usually, large flakes refer to +32 mesh, +50 mesh, +80 mesh, and +100 mesh flake graphite. Flake graphite below these meshes is called Fine flake graphit
Request a quote
Natural graphite is divided according to crystal diameter, usually divided into crystalline graphite (crystal diameter greater than 1 μm) and cryptocrystalline graphite (crystal diameter less than 1 μm). Crystalline graphite generally refers to flake graphite, according to its different particle size, divided into large flake graphite (crystal diameter greater than 147 μm) and small flake graphite (crystal diameter less than 147 μm). Compared with other types of graphite, although the grade of flake stone ink is not high, it has good floatability, plasticity, and lubricity, through repeated grinding and multiple separation, enrichment, and other methods, to obtain a higher grade of graphite concentrate, carbon content can generally reach 80%~99.5%, has high industrial application value.
In this paper, several purification methods of flake graphite are compared and analyzed according to the characteristics of flake graphite, the advantages and disadvantages of existing methods are discussed in detail, and some suggestions on the purification technology of crystalline graphite are put forward, which can provide a reference for the study of flake graphite in the future.

With the increase of fixed carbon content, the purity of flake graphite also increases, its application value also increases, so it is very necessary to purify graphite. The impurities in flake graphite are directly related to the producing area of graphite. The content and types of impurities are different in different producing areas. But its main impurities are potassium, sodium, magnesium, calcium, aluminum silicate minerals. The industrial purification process needs to select the best purification scheme according to the impurities in graphite ore, in order to obtain the best purification effect, therefore, the study of the flake graphite purification method is very important.
According to the physical and chemical changes in the flake graphite purification process, graphite purification methods can be divided into wet purification methods and fire purification methods. Wet purification method includes flotation method, acid, and base method, hydrofluoric acid method; Fire purification methods include chlorination roasting and high-temperature impurity removal. Industrial practice and experimental studies show that various graphite purification methods have different advantages and have their own market prospects.
The main problems of existing graphite purification technology are acid and alkali corrosion reaction equipment, purification byproduct or reaction reagent pollution to the environment, high energy consumption in the purification process, and high cost of special equipment. The problems mentioned above are determined by the characteristics of the purification method. In order to reasonably solve the various problems faced by the existing graphite purification, it is necessary to find a more ideal new method of graphite purification on the basis of the existing technology.
The reform and innovation of graphite purification technology are of great significance to the reasonable development and utilization of graphite resources, the transformation and development of the flake graphite industry, and the optimization of industrial structure. With the continuous expansion of the application range of graphite, especially the rapid development of new materials and new technologies, the industry is forced to higher and higher requirements for graphite purity index. High purity graphite, ultra-high purity graphite has been the development direction of the graphite deep processing industry in the future.

A large number of studies and production practices show that:
(1) Wet purification and fire purification methods in industrial production have advantages and disadvantages, using a single, conventional flake graphite purification method shows disadvantages and can not be extended; Simple method superposition, bring more technology, environment, and other problems, can not really solve the root of graphite purification problem.
(2) Flake graphite purification should be studied in depth from the aspects of improving purification efficiency, inhibiting secondary pollution, and reducing system consumption. By designing continuous operation scheme, developing efficient purification equipment, developing new environmental protection agents, optimizing raw ore pretreatment process, improving wastewater recovery and utilization rate, adding green environmental protection active agent and so on, Focus on solving the problems of complex technical processes, the high energy consumption of purification equipment, purification reagent pollution, waste of raw ore treatment, serious loss of water resources, some reaction conditions, such as caustic etching, reduce energy consumption, improve the transfer of graphite impurities to remove impurities and comprehensive resource recovery efficiency, to achieve sustainable development of environmental protection.
(3) Local thermal plasma graphite purification method in the induced gas discharge process, through the selection of different atmospheres, can form oxidation, neutral, reducing environment, and then activate the impurities in the graphite, play the role of neutralizing impurities. This method can be used with other methods to achieve a better purification effect, providing a new direction for the development of graphite purification technology, and establishing a new path for graphite purification.