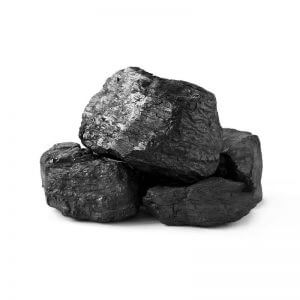
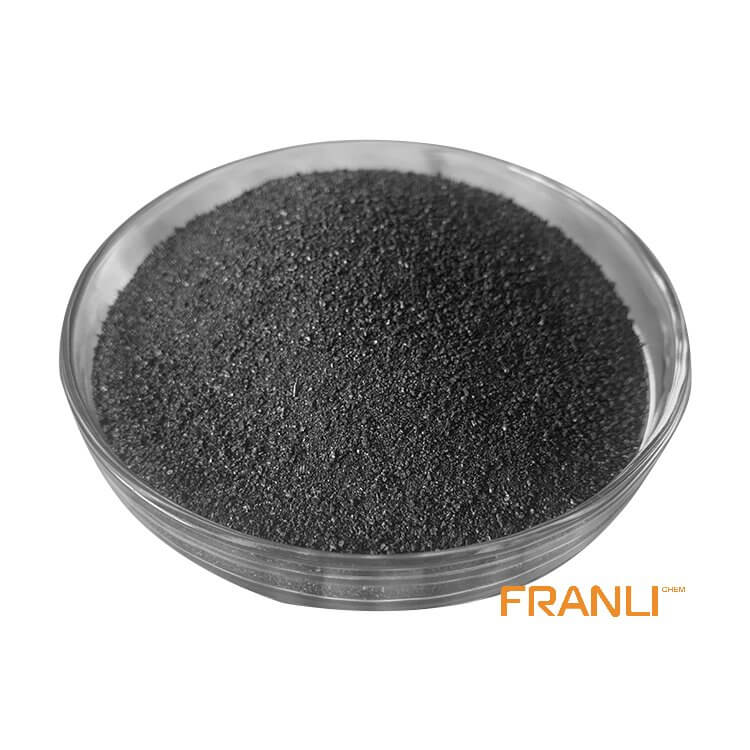
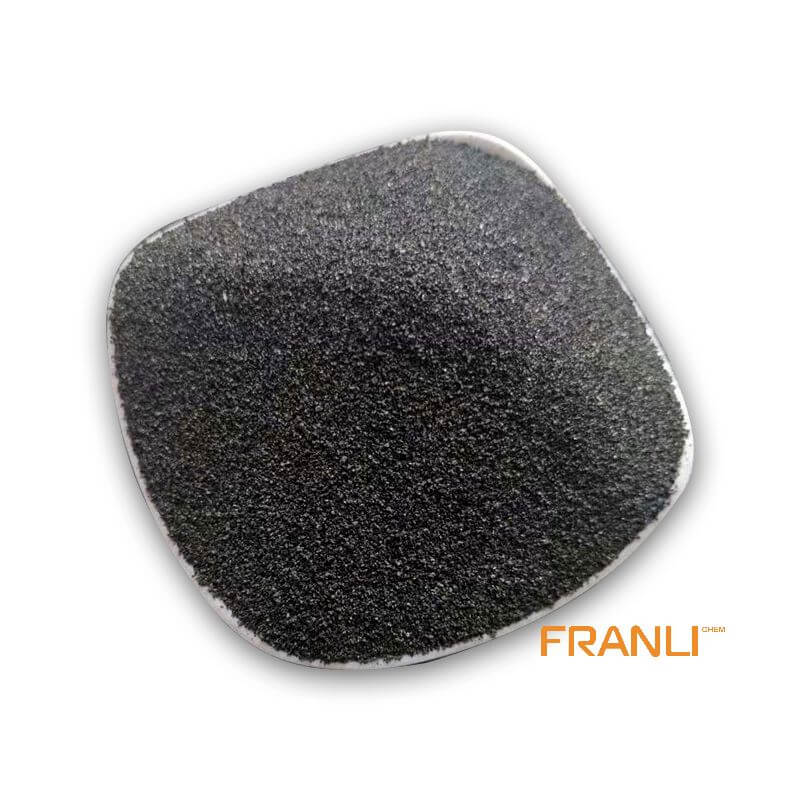
Petroleum Coke
Size
According to your requirements
Package
25 kg small bags into ton bags or ton bags
Features
Low ash content and low boiler ash discharge, etc.
Application
Depending on its quality, petroleum coke can be used in industries such as graphite, smelting and chemical industry, etc
Petroleum coke, as a byproduct of petroleum, is produced in the process of petroleum processing, that is, the crude oil is distilled to separate light and heavy oil, and the heavy oil is converted into petroleum coke by hot cracking. If petroleum coke can be obtained directly from petroleum processing, then the petroleum coke is raw coke or ordinary coke. Petroleum coke has irregular shape, dark gray or black, porous structure and metallic luster.
Request a quoteHigh-sulfur petroleum coke was commonly used, and it was widely used in cement manufacturing plants through rotary kiln calcination technology, which for many years led to problems such as crusting and environmental pollution in the high temperature zone of the firing system.
Therefore, now the cement industry generally promotes new technologies and technologies for environmental protection, and the right amount of sulfur is not only harmless in the cement production process, but also beneficial. To this end, the Franli factory took advantage of its high calorific value to partially replace fuel coal calcined cement clinker, so that high-sulfur petroleum coke opened up a new market in the cement industry.

Introduction of high sulfur petroleum coke
High sulfur petroleum has own unique properties. Its quality is directly related to the sulfur content of raw materials, according to petrochemical industry standards, the sulfur content of qualified products is not more than 3% in the product indicators of delayed coking petroleum coke. The appearance of high-sulfur petroleum coke is generally black lumpy with a slight metallic luster. Its structure is loose and porous, and it is easily crushed into fine particles.
60% of the ash is silica, followed by aluminum trioxide, in addition to a small amount of iron, calcium and trace amounts of vanadium, nickel, platinum, etc. These components do not pose a hazard to cement, and some elements also play a catalytic role in the conversion of sulfur during the firing of cement clinker.
Effect of petroleum coke on cement process
Petroleum coke exhibit its effect on the cement process, we can see that it show tremendous influence on fuel, as following:
(1) The influence of fuel: the cement production process, simply put, is “two grinding and one burning”, first mix various raw materials according to a certain ratio and grind into raw materials with fineness that meets the requirements, and then add water into balls and send them to the kiln to withstand high temperature calcination. The fired clinker is combined with an appropriate amount of gypsum and other materials, and then ground to become cement. Petroleum coke instead of coal calcined cement clinker must not bring obvious adverse effects in the entire cement production process, and the calcined cement fully meets the technical standards.
(2) The influence of infiltration into cement: raw meal pelletization is an important link in the production of vertical kiln cement, the quality of the quality will directly affect the output and quality of vertical kiln clinker, if completely use petroleum coke instead of coal, due to the influence of residual oil contained in it, the raw meal ball made of rough appearance and low strength (oil has hydrophobicity). After many trial and error, the use of improved petroleum coke as fuel can also produce qualified raw meal balls to meet the calcination requirements.

Environmental protection strategy of petroleum coke
Based on this fact that people focus on the environment protection all around the world, we should take actions when producing petroleum coke. Here are some suggestions we can do:
(1) The process of low-temperature raw meal separation to the kiln tail smoke chamber is adopted to quickly combine and condense the SO2 gas and cold raw material in the flue gas to prevent crusting.
(2) Optimize the design so that the structure of the decomposition furnace, burner and smoke chamber conforms to the combustion characteristics of petroleum coke.
(3) Pay attention to the characteristics of raw materials and production operations, select raw materials that meet the requirements of K^+ and Na^+ content, and control the fineness of petroleum coke powder and primary air volume.
Advantages of petroleum coke in cement plant
Here are some advantages of petroleum coke, such as:
(1) High sulfur petroleum has high coke calorific value, less ash and slightly higher volatile content, which can be used as a high-quality fuel for the production of vertical kiln cement.
(2) About 80% of the sulfur in petroleum coke can be converted into SO3 in the cement vertical kiln, which is absorbed by the clinker and plays the role of mineralizer in the process of clinker calcination. A small part is discharged outside the kiln in the form of SO2.
(3) It is completely feasible to use high-sulfur coke instead of part of the coal, and calcined cement clinker on a mechanized vertical kiln cement production line with perfect process conditions. After making appropriate adjustments to the production process and equipment, it can continuously produce high-quality cement for a long time, and the quality meets the requirements.
High-sulfur petroleum coke as a fuel for cement kilns is not only economically feasible, but also technically feasible. When the price of fuel coal is higher and the price of petroleum coke is low, it is more ideal to use it as the firing fuel. When using petroleum coke as firing fuel, environmental protection can be achieved by adjusting the sulfur content, and the firing and grinding systems can be adjusted and optimized accordingly, which can perfectly apply low-cost petroleum coke to the cement manufacturing industry.